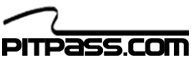
25/04/2016
NEWS STORY
Using Lewis Hamilton's Shanghai power unit failure as an example, Mercedes sheds light on how it assesses such failures.
What do we now know about the failure on Lewis' Power Unit in Shanghai?
The Power Unit in question arrived back at Brixworth in the early hours of Thursday morning of the week following the race and investigation into the failure has been on-going every minute since its return to the factory. The MGU-H has been stripped and the issue is suspected to be associated with the insulation. The turbocharger will be replaced in addition to the oil pumps, after debris was found in the oil system. With the repairs completed, this Power Unit will remain in the driver pool and travel to Sochi as a spare.
What's the initial course of action when a Power Unit failure occurs at the track?
First and foremost, a group of engineers at the circuit and a much larger group at Brixworth will pore through readings from the data logger, noting what every sensor on the Power Unit has recorded. That's an instant check which will quickly establish the severity of the problem.
What happens if a major fault is discovered?
If it's then determined that there is an issue which cannot be fixed at the track and hardware needs to be removed, the trackside technicians will ready the components for transport back to Brixworth as quickly as possible. The engineer responsible for the system suspected to be at the core of the issue will subsequently draw up a strip request instruction while the components are in transit.
What exactly does a strip request instruction involve?
It's a detailed sequence of instructions for the technicians working in the build department back at Brixworth, which outlines who will be allocated to each individual stage of the process, what specialist equipment and / or inspection techniques are required and which procedures need to be carried out. The list is written in chronological order with approximate time frames for each step to create a carefully considered timing plan that's fully resourced.
Where do the technicians begin when deconstructing a failed component?
In most cases, the technicians will start by back-flushing oil through the various galleries and filters of the oil and coolant systems to collect any fine debris. While larger fragments can be removed by hand, the finer debris - which often points to the start of the problem - can settle at the end of blind galleries or in filters downstream of the failed part.
How is debris analysed?
Microscope analysis of the debris is the first stage - looking at the different shapes and sizes present to establish whether it's a case of fine wear or a component which has shattered into small pieces. The debris will then be scanned with an electron microscope to check its chemical composition. This helps to establish the material type - which in turn provides an indication of the component that the debris might have come from.
What happens next to the various components in question?
Once the debris analysis has been completed and the components that were involved in the failure have all been stripped, everything is physically laid out to mimic its installed configuration. Looking at the series of components in front of them, what debris has been found and where it ended up, the engineers can begin to establish a likely sequence of events. They will then go back through the logged data from the track to find any step changes in the readings from each Power Unit sensor that might match up to a given theory.
Can virtual simulations be used in the investigation process?
Virtual simulation tools give a good insight into what's going on within a system and are used extensively throughout the development phase. When a component has failed, those models can be referred back to and changes made commensurate with what the team suspects has gone wrong to mimic the cause of the failure.
Does the team ever carry out physical simulations to re-create a failure?
Deliberate errors can be manufactured into hardware, which can then be tested on the dyno in an attempt to replicate a failure. This might be seen as an expensive means of testing - but it's cheaper than having a repeat issue at the circuit. Engines can be run with clearances altered to be either larger or smaller than the typical build standard tolerances - mimicking a scenario in which a surface has become worn, for example.
What about non-mechanical elements of the Power Unit?
Every element of the Power Unit can and will be analysed where necessary. An electrical component such as a PCB (Printed Circuit Board), for example, might be run in an oven at increasing temperatures to establish at what point its semiconductors stop working. This can then be tied in with knowledge about the temperature of that circuit board in the ERS module to establish whether overheating could be diagnosed as a cause of failure.
Who is generally involved in the diagnosis process?
In the first instance, an engineer with expertise in the system concerned will be assigned exclusively to investigating the issue through to its resolution. He or she will chair a meeting at least every 24hrs, calling in four to five people to help cogitate theories. These tend to be people that have a broad experience of the Power Unit, a good problem solving mindset and an ability for lateral thinking - working through theories step by step to ensure they are robust.