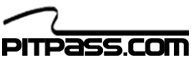
04/10/2005
NEWS STORY
![]() |
A1 Team Lebanon drivers Khalil Beschir and Basil Shaaban visited the Lola Group recently to see their chassis being repaired and take in a full factory tour of Lola's renowned technical facilities.
Beschir, who walked away from a spectacular accident at Paddock Hill bend after a collision with Italy's Enrico Toccocelo, was presented with the roll hoop shroud from his chassis by Lola Group managing director – Rupert Manwaring.
Lebanese motorsport has been put firmly on the motorsport map through their association with A1 Grand Prix and Beschir, who suffered no injuries in the 90mph barrel roll, was enthralled with his insight in to racecar design and manufacturer at Lola's Huntingdon base.
"The capabilities here are fantastic and it was fascinating to find out exactly how the A1 GP cars are made and how they are made with safety as well as speed in mind," said Beschir. "The first thing I thought of when I knew that the car was going to roll was 'don't worry, these cars are strong and I will be OK.' Now I know exactly how much hard work, skill and thought goes in to protecting us when things go wrong."
Getting an insight in to the Composites department at Lola and how the cars are built to withstand enormous forces was only part of the experience for Beschir and Shaaban. The pair also went on to view Lola's 50% scale state of the art rolling road windtunnel, modelshop and design department.
"The windtunnel was fascinating, as was the demonstrations of Lola's CFD (Computational Fluid Dynamics) and FEA (Finite Element Analysis) systems," said Basil Shaaban, who will share the seat with team mate Beschir throughout the A1 GP season. " The windtunnel itself is pristine and we were surprised to see an F1 team using the facility when we turned up."
Lola's windtunnel is commercially available and is used by a variety of prestigious companies throughout the year when not being used on Lola projects. Continuous investment in Lola's technical centre, which also incorporates a 7-post vehicle dynamic test rig, means that customers are guranteed excellent repeatability of results and reliability of operation.
The A1 Team Lebanon chassis was viewed by both drivers as it underwent repairs in Lola's Composite shop. Lola's senior composite engineer, Craig Turner and Composites Sales Manager Paul Jackson were on hand to explain the procedures of the repairs, which will be completed within 24 hours of the chassis arriving at the factory.
"Khalil's accident was quite unique in that his car touched down on a kerb after a substantial launch from the wheels of the other car," said Turner. "The damage to the roll hoop was actually quite minimal but obviously we replace any hoop that has been involved in such an accident. I would estimate that the car impacted the kerb at approximately 75-80 miles per hour before it then dissipated more energy by rolling through the gravel trap. In terms of design, the roll hoop is vital as a safety feature but the chassis and driver are also important in the overall packaging when it comes to ensuring that these accidents are survivable in modern racing. The hoop itself is actually bonded on to the chassis using an epoxy resin system called 3M 9323."
![]() |
Lola's experience in composites and FEA applications is instrumental in providing teams and drivers with safe and strong racing cars. As Craig Turner explained to Khalil and Basil during their visit, it is all about meticulous study and attention to detail that contributes to Lola's excellent safety record in International motorsport throughout so many different racing disciplines.
"We use FEA to analyse every layer of carbon fibre within the design of structural components," continued Turner. "In regard to the roll hoop structure we utilise MSC Patran in conjunction with Laminate modeller to drape each and every ply of carbon onto the surface. Fibre angles can readily change direction around complex geometry and it's vital when designing such structures to accurately ascertain where the peak strains occur."
Before the A1 GP cars turned a wheel they undertook the stringent FIA crash testing procedures, which see static loads of 7.9 tonnes unleashed on to the roll hoop that combines longitudinal, transverse and vertical loads. The A1 GP roll hoop, as well as the rest of the chassis passed these tests with flying colours but the hoop, although relatively simple in design, has added safety features that are unseen to the naked eye.
"Because the hoop is designed solely in carbon fibre and often impacts on a hard surfaces such as tarmac or indeed in this instance a kerb or rumble strip, we utilise a small metal plate in the top of the structure which protects the hoop against abrasion when a car is inverted for a period of time," said Turner. "This plate is encapsulated in to the first two layers of composite material within the hoop and helps to maintain the structural integrity during an accident. Although it is not a dynamic part of the hoop design, in our experience it is a necessary additional safety feature within the design."
This was proven after examination of Beschir's roll structure after the accident.
After meeting and posing for photographs with members of Lola's composites and design staff, Khalil and Basil returned to their Oxford base to prepare for the next round of the A1 Grand Prix series at Lausitzring in Germany this weekend.
The A1 Team Lebanon seat is held by Tameem Auchi and was launched in Beirut earlier this year with the country's President Emile Lahoud in attendance. Beschir, was running an impressive 7th before the accident.