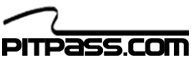
08/06/2004
NEWS STORY
Pat Symonds
Formula 1 cars, in common with military aircraft and a few of the more modern passenger aircraft, use a brake material that is significantly different to what we find on road cars. A typical road car uses a cast iron brake disc with an organic brake pad. In an F1 car, though, the same material is used for both disc and pad, and this material is known as carbon-carbon - a significantly different material to the carbon-fibre composites used in the rest of the car. Carbon-carbon is essentially a pure form of carbon and is both extremely light (approx. 50% of the weight of standard materials) and also possesses a higher coefficient of friction at the correct operating temperatures. This peaks at around 0.6, compared to 0.3 for conventional materials.
Manufacturing carbon-carbon discs is a lengthy process which takes hundreds of hours, and involves the materials being heated to 2500°C. The complexity of the procedure also explains the other major property of carbon-carbon brake discs and pads: cost. A set of brake discs (four) costs $4500, while a set of pads (eight) is $2400, and the team will use over 200 discs in a year, and double the number of pads.
When we assess brake performance, we do so largely in terms of two parameters: bite and consistency. Bite is the initial friction experienced when the driver first presses the brake pedal and the brakes are not yet at the correct operating temperature. Consistency is a measure of how consistent the friction is for the duration of the braking period. Carbon-carbon brakes possess very particular properties, A carbon brake has relatively poor performance below about 400°C and has optimum braking performance above 650°C. Unfortunately, whereas conventional brakes wear down through the normal mechanism of wear that any frictional material experiences, a carbon brake not only suffers wear through this mechanism but also a process called oxidisation. Oxidisation is in simple terms a burning of the surface of the disc, and at temperatures above 600 degrees C it is accelerated and becomes the main mechanism of wear. Bearing in mind that during a braking event the temperatures of the brake discs will reach around 1200 degrees C, it can be seen that oxidisation is extremely significant in the brake wear process. On the straights of course, the brake ducts are feeding air to the brakes and so they drop below the oxidisation temperature but as they still maintain these high temperatures for a relatively long time, paradoxically the very air that is being used to cool them contains a high amount of oxygen that accelerates the wear process.
The other factor that is very circuit-dependent is the cooling of the brakes. The brakes on all racing cars are cooled by forcing air through the ducts and blowing it both through the radial centre vents of the disc itself and also over the surface of the pads and discs. The amount of air is controlled by using different size ducts and for a heavy braking circuit such as Montreal, we are forced to use some of the biggest ducts of the season. Moving from the smallest to largest cooling ducts can cost 1.5% in aerodynamic efficiency, which represents a loss of 1 kph in top speed. Indeed, the size of the ducts is not driven simply by aerodynamic objectives: smaller ducts are used at circuits which demand less braking in order to manage the temperatures of the brakes and achieve the correct balance between high performance and acceptable wear rates.
When an experienced racing driver first drives an F1 car, almost without exception, their first comment concerns the power of the brakes. A modern F1 car can achieve 5.5g under braking whereas even a high-performance road car will probably not reach 1g. Furthermore, F1 cars don't use power brakes so the driver has to press the pedal extremely hard to produce the brake pressure (up to 100 bar). Of course, when the brakes are first applied at 330 kph the car has very high downforce and consequently it is not possible to lock the wheels. However as the car slows down, not are the downforce and hence tyre grip reduced but also the brakes start coming into their optimum range: thus, the ability to transmit braking force effectively to the road reduces as the actual braking power increases.
If the driver were to maintain the very high pedal forces it would not be long before the wheels locked, so the driver needs to modulate the brake pedal pressure to try and keep the wheels just at the point of locking. Unlike road driving, where braking is ideally all in a straight line, a racing driver will brake deep into the corner to try and reduce his lap-times. As the car experiences the combined braking and cornering forces, it is very easy to lock the inside front wheel. This would make the car understeer and miss the apex so again the driver needs to modulate his braking in order to avoid this. It is also interesting that while and F1 car has very high levels of downforce, it also has around 2.5 times the drag of a normal road car and at maximum speed, just lifting off the throttle without touching the brakes can cause deceleration of around 1g.
Achieving braking performance alone is easy, as is minimising the aerodynamic penalty, but the secret, as ever in Formula 1, is to achieve maximum braking performance and minimum aerodynamic losses simultaneously. This is where Canada poses its real challenge, combining very low speed corners and chicanes with long straights - thus, both braking performance and aerodynamic efficiency are at an absolute premium. Furthermore, with low levels of downforce on the car, it is generally more nervous under braking, exactly what a driver doesn't want when he is looking for confidence and stability as he decelerates. Managing these challenges, both from the engineering and driving points of view, is one of the keys to a successful weekend in Montreal.
Denis Chevrier
The Circuit Gilles Villeneuve in Montreal is known for two things: braking, and engine torque. The pattern of any lap is relatively simple - you need to be able to build up a lot of speed very quickly, then shed it even faster for the tight corner that inevitably follows.
Indeed, in spite of the high maximum speeds we see the cars reach there (the third highest of the season), Montreal is not actually a particularly demanding circuit in terms of the standard parameters by which we measure a circuit's difficulty. The engine only spends 58% of the lap at full throttle, while the longest period at full throttle is 13 seconds, almost identical to the season average.
Rather, the challenge at Montreal comes in the form of the extremes at which the engine is required to operate. Not only do we record the third-highest maximum speeds of the year at this circuit, but it also sees the third-lowest engine speed of the year, in the hairpins. In terms of the breadth of performance an engine requires, Montreal is actually comparable to Monaco, but with slightly higher values in all areas.
As such, a good engine in Canada needs to be a complete engine, without any weaknesses. It needs good power, but also driveability through the chicanes and good torque for launching out of the slower corners. In all of these areas, the RS24 constitutes a significant advance on last year's engine.
Aside from these basic challenges, the circumstances and location of the circuit can also provide challenges for the engineers. The back straight prior to the final chicane can suffer from headwinds which make the calibration of the final drive difficult, while leaves and circuit debris have caused cooling problems in the past.